Danieli Automation S.p.A.
Via B. Stringher, 4
33042 Buttrio (UD) – Italy
Phone (+39) 0432 518111
Fax (+39) 0432 673177
E-mail info@dca.it
P.IVA 00162990303
3Q TECHNOLOGY
GRUPPO RIVA
THY MARCINELLE
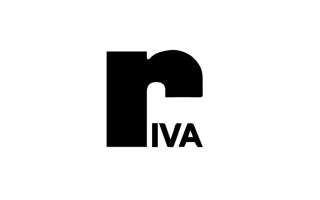
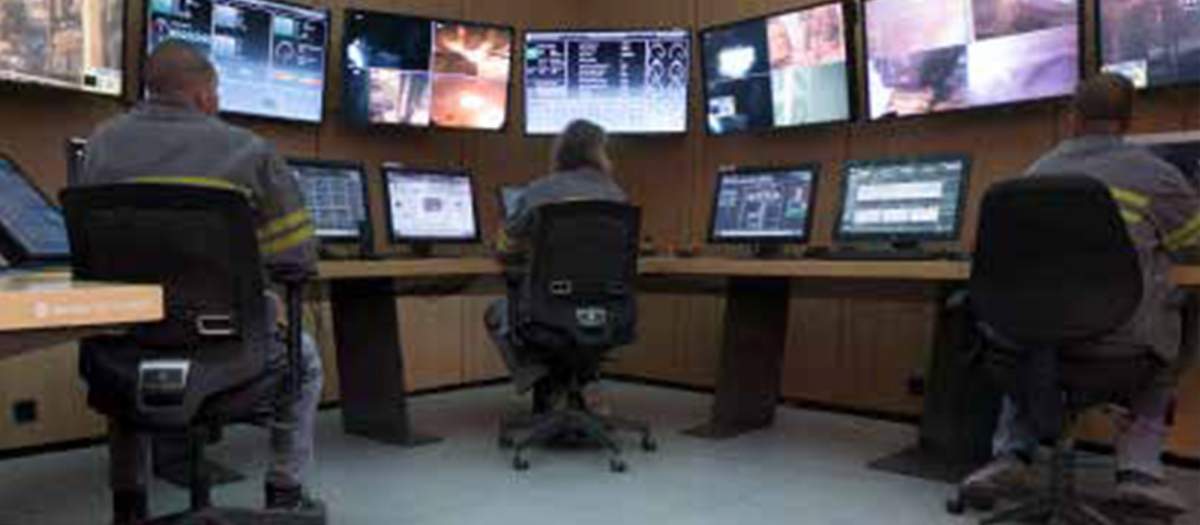
The customer
Riva Group is Italy's largest steel producer and the fifth biggest player in the European steel industry. Founded in 1954, the group has specialized in the manufacturing of long products using electric arc steelworks, achieving an international leadership in the main european countries, thanks to high production standards and to a focused and steady strategy of growth and investments. It has 20 industrial plants located in the following countries: six in Italy, seven in France, three in Germany, two in Belgium, one in Spain and one in Canada. Riva Group supplies different product areas, some of which, for example mechanics engineering, automotive and earth-moving machines, demand especially high quality standards. Production includes drawn, peeled and ground steel items derived from further cold-rolling processing.
Riva Thy Marcinelle steelmaking plant is located in Charleroi, Belgium, and it consists of:
> 160-t electric arc furnace, enclosed in a doghouse;
> ladle furnace;
> eight-strand conticaster for billets;
> pusher-type reheating furnace;
> a two-strand bar and wire rod mill for reinforced concrete;
> two lines for cold rolling and straightening for concrete reinforcing rounds.
Riva Thy Marcinelle steelmaking plant is located in Charleroi, Belgium, and it consists of:
> 160-t electric arc furnace, enclosed in a doghouse;
> ladle furnace;
> eight-strand conticaster for billets;
> pusher-type reheating furnace;
> a two-strand bar and wire rod mill for reinforced concrete;
> two lines for cold rolling and straightening for concrete reinforcing rounds.
The challenge
The vision of the Riva Group and the solutions developed by Danieli Automation are come together at the Thy Marcinelle plant. This system upgrade paves the way to a new concept of control for the steel industry, for improved plant performances and reduced dependence on the skill of operators.
This concept has led to develop a new generation of operator interface and pulpit design, to make operators work more safely, efficiently, and easily.
This pulpit matches very well the requests from the Riva Group. At the Thy Marcinelle plant Danieli Automation has won the opportunity to create a unique and revolutionary workspace where the operators don’t see the plant through windows, but rather watch huge screens and apply a new system approach.
This concept has led to develop a new generation of operator interface and pulpit design, to make operators work more safely, efficiently, and easily.
This pulpit matches very well the requests from the Riva Group. At the Thy Marcinelle plant Danieli Automation has won the opportunity to create a unique and revolutionary workspace where the operators don’t see the plant through windows, but rather watch huge screens and apply a new system approach.
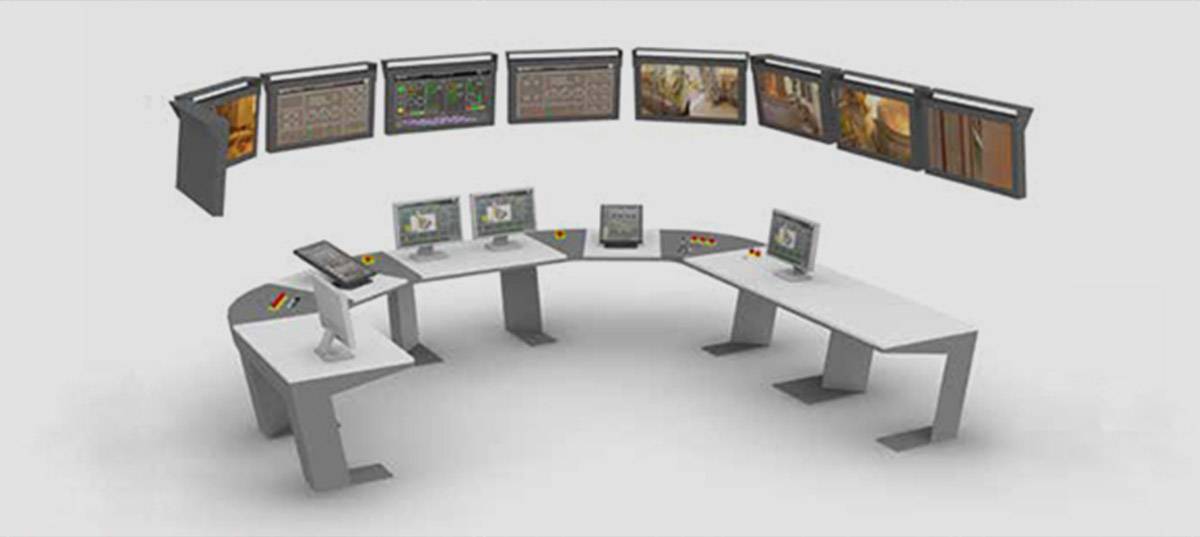
The solution
The solution adopted by Riva Thy Marcinelle with Danieli Automation is to unify and integrate the control pulpit of the EAF with the one of the LF. The new control station is defined by a room without windows, in order to control two different technological processes. The new 3Q automation control pulpit is comprised of:
> Operator Assistant;
> Human Machine Interface;
> Area Performance Indicator;
> Plant Performance Indicator.
The additional goal of this project was to increase the plant’s output by 0.5 heats/shift to reach 14 heats during each 12-hour shift. The commissioning phase was divided into three stages:
> Operator Assistant;
> Human Machine Interface;
> Area Performance Indicator;
> Plant Performance Indicator.
The additional goal of this project was to increase the plant’s output by 0.5 heats/shift to reach 14 heats during each 12-hour shift. The commissioning phase was divided into three stages:
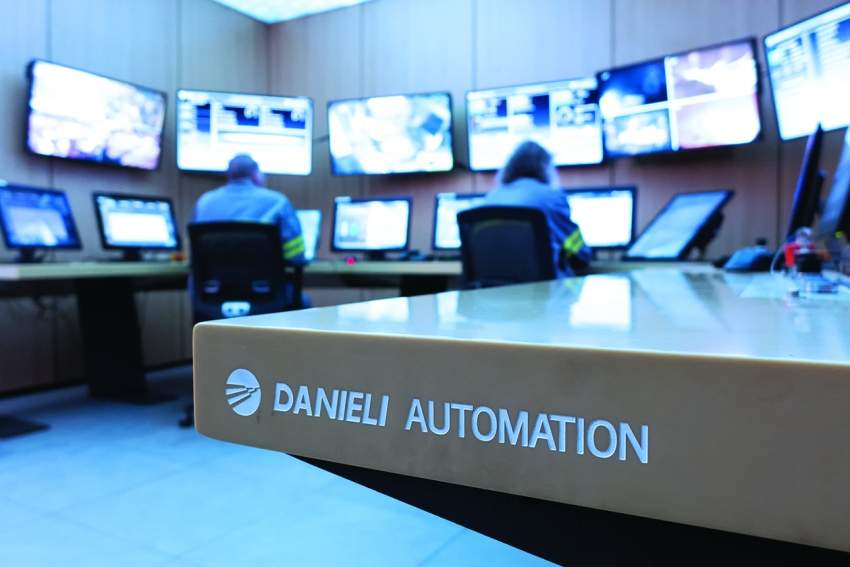
The benefits
The Danieli Automation upgrade, with a single, unified control pulpit for EAF and LF, optimized performances by reducing delays and decreasing power-off time. Both Riva Thy Marcinelle and Danieli Automation are well satisfied with the results of the revamping. The new system had sensibly decreased the unscheduled delays during production, and therefore the power-off of the furnace has been reduced. The Auto-Pilot and the advanced messaging system guide the operator throughout all melting and refining phases. While in the past the production of 14 heats was only occasionally achieved and always close to the end of a shift, now it is possible to complete the 14th heat even 30 minutes before the end of it. Moreover, the enhanced reporting system allows the meltshop department manager to control each day’s results and to tune the process to increase the level of production. Riva Thy Marcinelle recognized that over a long period there are margins to achieve even better performances, and officially expressed its appreciation to Danieli Automation for a job well done.
To confirm this performance improvement, a numerical comparison has carried out between the two best results obtained before and after 3Q system implementation. As described in Table 2, the time required to get 27 heats (13+14) in a double shift has been 24 hours and 20 minutes, with an average time overrun of 10 minutes per shift for a final target of 14 heats for single shift. The new system performance after 3Q installation clearly shows that during a single shift, 14 heats have been produced in less than 12 hours.
The result was obtained without mechanical or process interventions and this can be deduced by power-off decrease from 13 to 9 minutes, thanks to average delay reduction per heats. This phenomenon is also confirmed by Graph 3, showing the good effect of the launch of all the functionalities of the Autopilot system, along with the huge introduction of overlapping cycles, in the reduction of overall delays caused by automation. In particular, percentage of delays due to process automation failures goes from 20% to 2% after new 3Q functionality introduction.
To confirm this performance improvement, a numerical comparison has carried out between the two best results obtained before and after 3Q system implementation. As described in Table 2, the time required to get 27 heats (13+14) in a double shift has been 24 hours and 20 minutes, with an average time overrun of 10 minutes per shift for a final target of 14 heats for single shift. The new system performance after 3Q installation clearly shows that during a single shift, 14 heats have been produced in less than 12 hours.
The result was obtained without mechanical or process interventions and this can be deduced by power-off decrease from 13 to 9 minutes, thanks to average delay reduction per heats. This phenomenon is also confirmed by Graph 3, showing the good effect of the launch of all the functionalities of the Autopilot system, along with the huge introduction of overlapping cycles, in the reduction of overall delays caused by automation. In particular, percentage of delays due to process automation failures goes from 20% to 2% after new 3Q functionality introduction.