DANIELI AUTOMATION NEWS
2017, 22nd March
Danieli Service chock reconditioning for flat product rolling mills
The most cost-effective solution for work roll and back-up roll maintenance of hot and cold mills.
Maintaining rolling mills is difficult, costly, and time-consuming, but the alternative may be even worse for the mill operators. Without regular inspection and maintenance, rolling mill equipment can deteriorate to the extent that any costs saved by avoiding maintenance becomes insignificant in comparison to the increased downtime and product quality problems resulting from premature equipment failures.
Neglected back-up roll chocks may be found in strip mills around the world. Bore concentricity or ovality, coupled with excessive clearances resulting from wear and fretting corrosion of sliding surfaces can escalate quickly, leading to premature bearing failures. The further result is poor product quality, seen specifically in the strip surface conditions, and shape and profile tolerances.
Danieli provides critical support services for inspection and maintenance to rolling mill operators worldwide. Applying the latest inspection, refurbishment, and manufacturing techniques for 3D laser measurement, weld or metal spray cladding, and CNC machining (for example).
Danieli’s worldwide facilities refurbish and repair badly damaged, worn and deformed chocks, cost-effectively, restoring them to original design tolerances to match their own best mill performances.
A detailed inspection and condition report is provided for every chock, together with options for restoration, enabling the rolling mill operator to take informed decisions to address operating cost and finished product quality.
Danieli draws on many decades of knowledge and experience as a rolling mill designer and builder, using these resources to identify opportunities for saving operating costs and improving profit margins by introducing the latest technologies during the process.
For more info:
Keith Shillam
k.shillam@danieli.it
+39 0432 195 5647
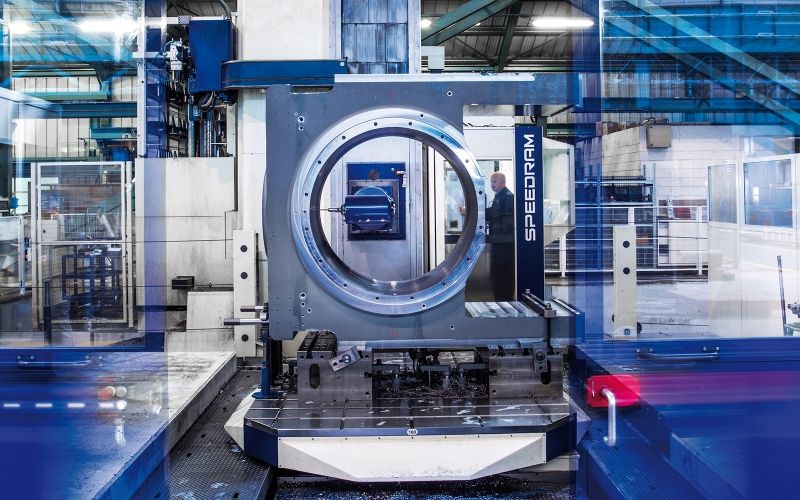
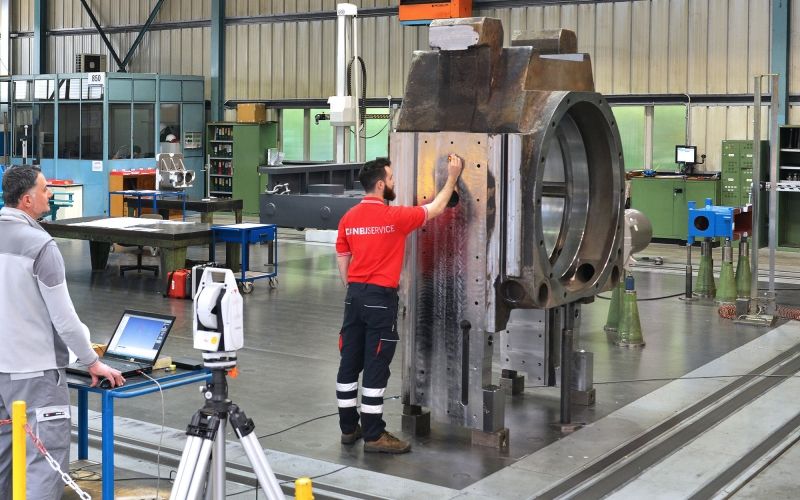